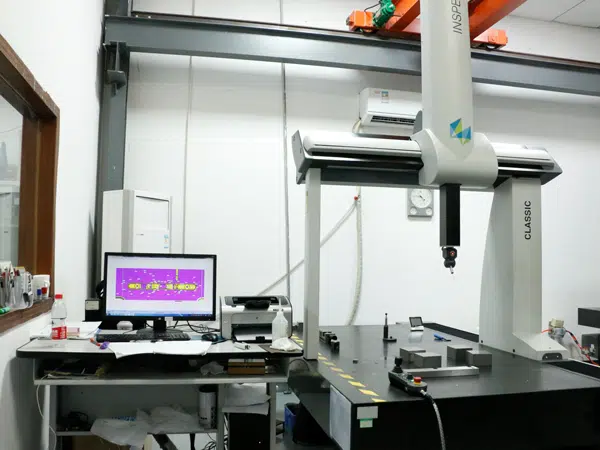
CNC machining stands at the forefront of modern manufacturing, enabling the creation of intricate and highly precise components. With its remarkable level of detail, CNC machining is revolutionizing numerous industries, from aerospace and automotive to medical and consumer electronics. By precisely controlling cutting tools, CNC machines can fabricate parts with exceptional dimensional tolerances, intricate geometries, and surface finishes that meet the demanding requirements of contemporary technology.
- Moreover, CNC machining offers unparalleled precision, ensuring that components are produced to exacting specifications every time.
- This, manufacturers can depend upon CNC machining to create high-quality, reliable products with minimal defects.
In conclusion, precision CNC machining is an essential technology for shaping tomorrow's advancements. Its ability to produce complex parts with exceptional accuracy and consistency makes it an indispensable tool for driving progress across a wide range of industries.
Unlocking Design Freedom with CNC Milling
CNC milling empowers the design process by providing unparalleled precision and flexibility. With its ability to carve intricate geometries from a variety of materials, CNC milling opens a world of possibilities for engineers, designers, and makers alike. From rapid prototyping to high-volume production, CNC milling provides exceptional accuracy and repeatability, ensuring that every part meets the highest standards.
This technology facilitates the creation of complex designs that would be impossible to achieve with traditional machining methods. With its wide range of tooling options and cutting strategies, CNC milling can accomplish a diverse set of tasks, including drilling, tapping, engraving, and 3D modeling.

The flexibility of CNC milling makes it an ideal solution for a broad spectrum of industries, from aerospace and automotive to medical and consumer goods. Its ability to tailor designs to specific requirements empowers businesses to innovate and create products that stand out in the marketplace.
CNC Turning: The Art of Rotational Precision

CNC turning is a advanced manufacturing process that utilizes computer-controlled machines to create metal parts by rotating them at high speeds against a cutting tool. This process allows for intricate and complex designs to be achieved with exceptional accuracy and repeatability.
The lathe, the heart of CNC turning, is equipped with a variety of tools that can mill away material to create desired geometries. Programs, often written in CNC code, guide the machine's movements, dictating the speed, depth, and direction of the cutting tool.
From small parts to large structures, CNC turning plays a vital role in fields such as aerospace, automotive, and medical manufacturing. Its ability to produce high-quality parts with tight tolerances has made it an indispensable tool for modern manufacturing.
Advanced CNC Programming Techniques
Mastering expert CNC programming techniques is crucial for achieving optimal results in modern manufacturing. These techniques encompass a wide range of strategies and methodologies aimed at maximizing toolpath efficiency, optimizing material removal rates, and ensuring precise component fabrication. Skilled programmers leverage complex G-code structures, specialized commands, and innovative strategies to generate highly accurate and efficient machining programs. By implementing these advanced techniques, manufacturers can significantly improve production speed, reduce material waste, and enhance the overall quality of their manufactured products.
- One essential technique is parametric programming, which allows for dynamic adjustments to machining parameters based on real-time sensor data.
- Another powerful approach involves utilizing simulation software to predict toolpath behavior and identify potential collisions or interference issues before physical machining commences.
- Safeguarding strategies are paramount in CNC programming, ensuring the safe operation of the machine and preventing damage to tools or workpieces.
Continuous learning and exploration of novel CNC programming techniques are essential for staying at the forefront of this rapidly evolving field. By embracing these advanced methodologies, manufacturers can unlock new levels of precision, efficiency, and productivity in their machining operations.
Enhancing CNC Machining Processes for Efficiency
To achieve peak output in CNC machining, meticulous fine-tuning of processes is paramount. This entails scrutinizing every aspect, from selecting the right tools and machine settings to workpiece fixturing and material characteristics. Implementing best practices such as regular maintenance on CNC machines, utilizing advanced simulation software, and continuously monitoring machining processes can significantly reduce cycle times, improve surface finishes, and ultimately enhance overall effectiveness.
- Implementing a robust quality control system
- Investing in skilled operators
- Optimizing workflow and material handling
The Future of Manufacturing: CNC Automation
The manufacturing sector continues to evolve rapidly, driven by the need for increased efficiency, precision, and productivity. A key trend shaping this evolution is the adoption of Computer Numerical Control (CNC) automation. CNC machines deliver unparalleled accuracy and repeatability, enabling manufacturers to produce complex parts with remarkable consistency. As technology advances, CNC automation has become even more sophisticated, incorporating capabilities such as 3D printing and robotics. This fusion of technologies presents to transform the future of manufacturing by automating complex processes and enabling new levels of efficiency and customization.
Choosing CNC Machined Materials

Dive into the realm of CNC machining and discover the expansive variety of materials that can be transformed by this precise manufacturing process. From robust metals like aluminum, titanium, and stainless alloy, to versatile polymers such as ABS, polycarbonate, and acrylic, CNC machining offers a wide palette for fabrication. This comprehensive guide explores the properties of common CNC machining materials, helping you select the optimal choice for your project's specifications.
- Delve into the unique characteristics of each material type.
- Uncover the ideal applications for various CNC machining materials.
- Choose informed decisions based on factors like strength, durability, and appearance .
Whether you're crafting intricate prototypes or producing large-scale components , understanding the nuances of CNC machining materials is essential for achieving optimal results.
Understanding G-Code: The Language of CNC Machines
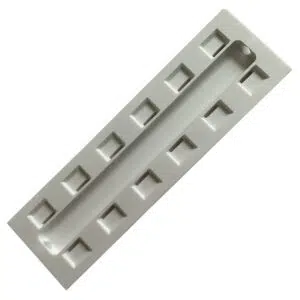
G-code serves as the fundamental blueprint utilized by Computer Numerical Control (CNC) machines. This textual program provides precise commands to guide the movements of CNC elements, enabling the manufacture of intricate designs with exceptional accuracy.
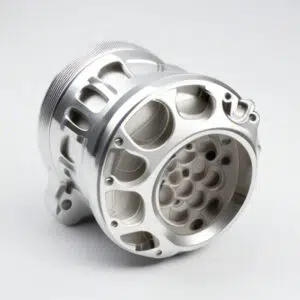
Each line of G-code represents a collection of instructions that dictate the orientation of the CNC head, its speed, and other settings. CNC operators develop these G-code programs, meticulously determining every movement required to transform raw materials into the desired result.

The versatility of G-code enables CNC machines to produce a diverse range of objects, from simple components to complex assemblies.

Understanding the fundamentals of G-code is therefore vital for anyone engaged in the domain of CNC machining.
Troubleshooting Common CNC Machining Issues
CNC machining can present a wide array of challenges for even the CNC machining most experienced operators. One common difficulty is tool wear, which can lead to inaccurate cuts and surface finish imperfections. In order to address this, it's crucial to frequently inspect tools for signs of damage and substitute them as needed.
Another frequent complaint is chatter, a high-frequency vibration that can influence the quality of your workpiece. Chatter often occurs when the cutting parameters are not adjusted properly. To mitigate chatter, try raising the feed rate or adjusting the depth of cut.
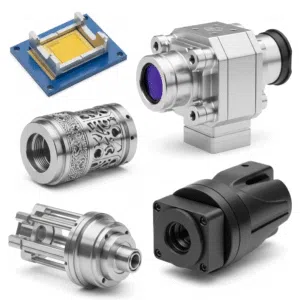
Some other common CNC machining issues include:
* Incorrect G-code programming
* Inadequate clamping techniques
* Material defects
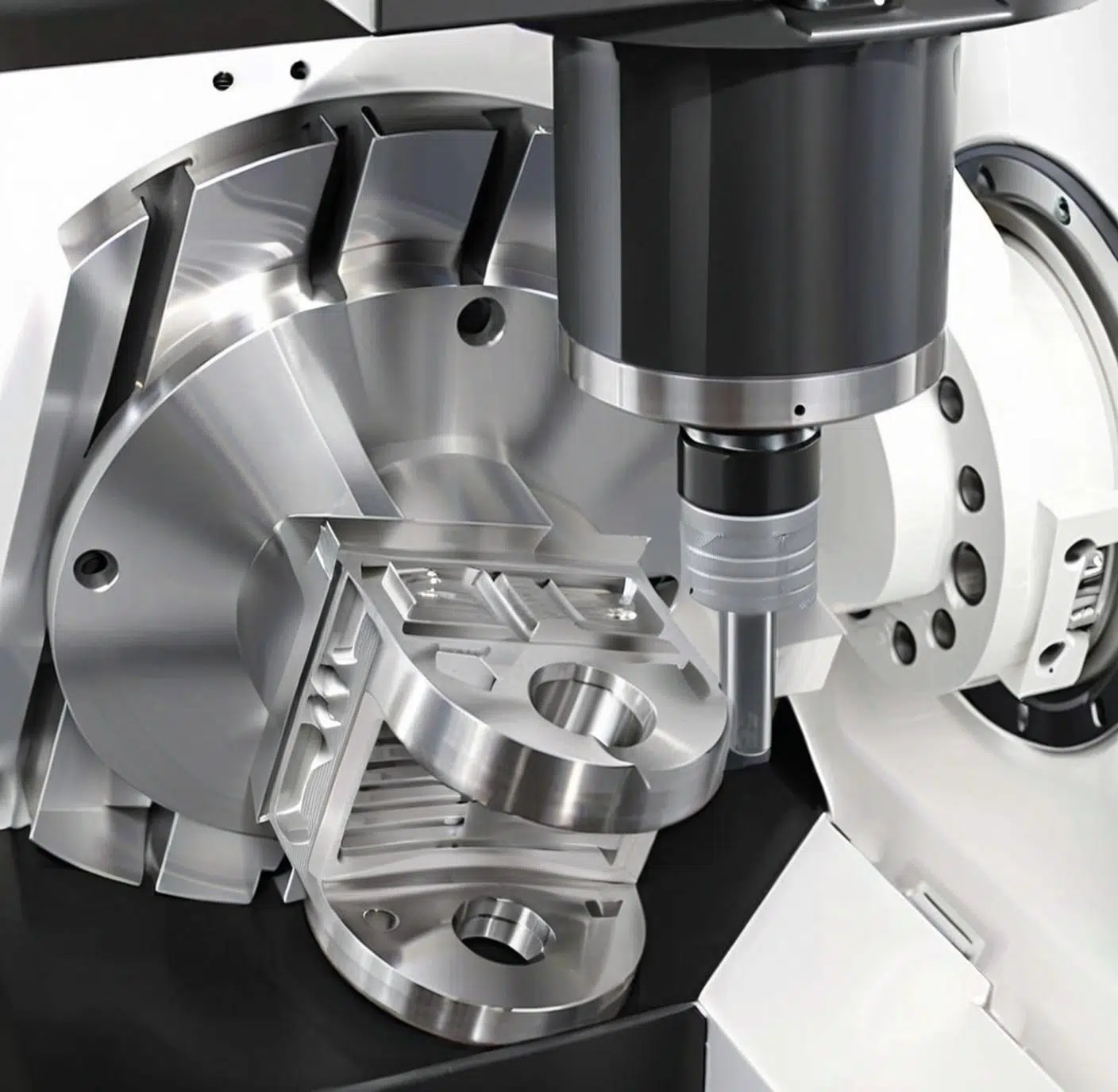
Proper troubleshooting and maintenance can assist you overcome these challenges and achieve optimal CNC machining results.
CNC Prototyping: Rapid Design Iteration
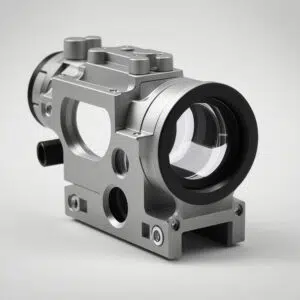
In today's fast-paced design world, the ability to rapidly iterate designs is paramount. CNC prototyping provides a powerful solution, enabling designers and engineers to quickly produce physical samples based on their latest designs. This rapid iteration process allows for quick feedback, leading to faster product development cycles and ultimately, more successful results.
- Advantages of CNC prototyping include:
- Exceptional accuracy and repeatability, ensuring that prototypes closely reflect the final design.
- Quick turnaround times, allowing for frequent iterations and testing.
- Economical compared to traditional manufacturing methods, especially for low-volume production runs.
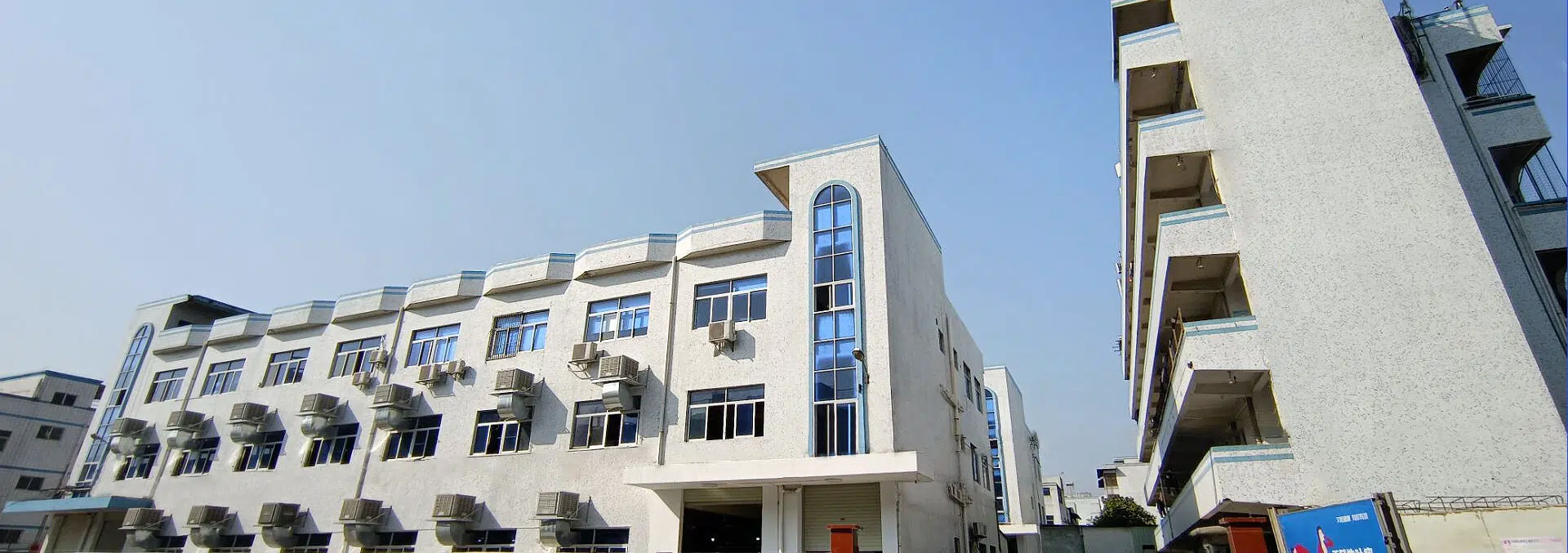
High-Speed Machining with CNC: Pushing the Limits
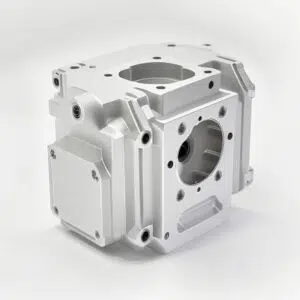
High-speed machining utilizes CNC technology to achieve remarkable rates of material removal. This process permits manufacturers to produce intricate components with remarkable precision and efficiency. By employing high-speed cutting tools and optimized machining parameters, complex geometries can be produced with minimal tool wear and heat accumulation. The result is a significant increase in productivity while maintaining the highest quality of surface finish.
- Additionally, high-speed machining decreases cycle times, enabling faster turnaround and boosted production output.
- As a result, manufacturers can meet the growing demands of industries such as aerospace, automotive, and electronics, where rapid prototyping and production are essential.
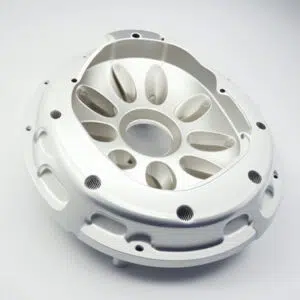
Surface Quality and Precision in CNC Machining
In the realm of CNC machining, achieving optimal surface finish and accuracy plays a crucial role for ensuring product quality and functionality. The meticulous control exerted by computer numerical control (CNC) machines allows for precise material removal and manipulation, resulting in surfaces that meet stringent specifications.
Multiple factors influence the final surface finish achieved through CNC machining, including cutting tool selection, feed rates, spindle speeds, work material characteristics, and machine calibration. Employing appropriate cutting strategies and optimizing these parameters can significantly enhance surface roughness, smoothness, and dimensional accuracy.
- Reaching a high level of surface finish is frequently measured in terms of surface roughness (Ra), which quantifies the deviation from an ideal smooth surface. Lower Ra values indicate smoother surfaces, while higher values reflect increased surface irregularities.
- CNC machines are capable of producing a wide range of surface finishes, from highly polished to rough textures depending on the desired application and material being machined.
- Accurate machining requires meticulous attention to detail throughout the entire process. This includes ensuring proper tooling alignment, workpiece clamping, and consistent machine operation to minimize errors and achieve precise dimensional tolerances.
By mastering the intricacies of surface finish and accuracy in CNC machining, manufacturers can produce components that meet the demands of various industries, ranging from aerospace and automotive to medical and electronics.
CAD/CAM Integration
In the realm of modern manufacturing, optimizing for CNC production has become paramount. This is where the synergy between Computer-Aided Design (CAD) and Computer-Aided Manufacturing (CAM) emerges as a game-changer. By harmonizing these two powerful technologies, manufacturers can achieve unprecedented levels of precision, productivity, and cost-effectiveness.
- CAD software
- generate detailed digital models that serve as the blueprint for CNC machining.
- CAM software
- translate these CAD designs into precise g-code for CNC machines to execute.
This direct data exchange minimizes the need for manual intervention, thus reducing errors. Furthermore, CAD/CAM integration supports real-time design modifications, allowing manufacturers to adapt quickly to evolving customer demands or production requirements.
From Blueprint to Finished Part: The CNC Journey The Exciting Transformation from Design to Reality
A computer numerical control milling process is a sophisticated blend of technological innovation and precision engineering. It begins with a blueprint, meticulously crafted by designers who envision the final product. This virtual representation serves as a roadmap for the CNC machine, which interprets the instructions encoded within it.
The machine's powerful rotating tool cuts into a block of raw material, removing excess substance with remarkable accuracy. Each movement is precisely controlled by the CNC program, ensuring that the final part meets the original design specifications.
The journey from blueprint to finished part is a testament to the power of technology. CNC machining has revolutionized manufacturing, enabling the creation of complex and intricate parts with unparalleled precision and efficiency.
How CNC Machining Drives Industry 4.0
Industry 4.0 is characterized by the fusion of physical and digital worlds, CNC machining leading to a paradigm shift in manufacturing processes. Key to this transformation is CNC machining, which has evolved into a highly automated and intelligent technology. With its ability to achieve precise fabrication, CNC machining plays a essential role in enabling the benefits of Industry 4.0.
CNC machines are increasingly equipped with sensors and software that allow for real-time data collection. This data can be used to optimize machine performance, predict servicing needs, and improve product quality. Moreover, the integration of CNC machining with other Industry 4.0 technologies, such as cloud computing and artificial intelligence, unlocks further opportunities for increased efficiency, flexibility, and customization.
- Additionally, the rise of additive manufacturing complements traditional CNC machining, allowing for complex geometries and on-demand production.
- This synergy of technologies empowers manufacturers to respond to evolving market demands with agility and precision.
Tailored CNC Machined Components: Parts
In today's dynamic manufacturing landscape, achieving precise and consistent components is paramount. This demand has fueled the rise of custom CNC machined components as a efficient solution for a wide variety of industries. From aerospace to automotive, medical devices and beyond, custom CNC machining allows manufacturers to produce parts with remarkable accuracy and repeatability.
Harnessing the power of computer-aided design (CAD) and computerized numerical control (CNC), skilled machinists can shape raw materials into intricate components that meet specific specifications. This technique offers numerous advantages, including optimized performance, improved durability, and the ability to implement complex geometries.
- Additionally, custom CNC machining allows for small-batch production, making it an ideal choice for prototyping, low-volume manufacturing, and specialized applications.
- Opting a reputable CNC machining provider with experience in your sector is crucial to provide the highest standard of components.
Ultimately, custom CNC machined components provide designers with a powerful tool for enhancing innovation and meeting the ever-evolving demands of modern manufacturing.
CNC Machine Tool Selection
Acquiring the perfect CNC machine